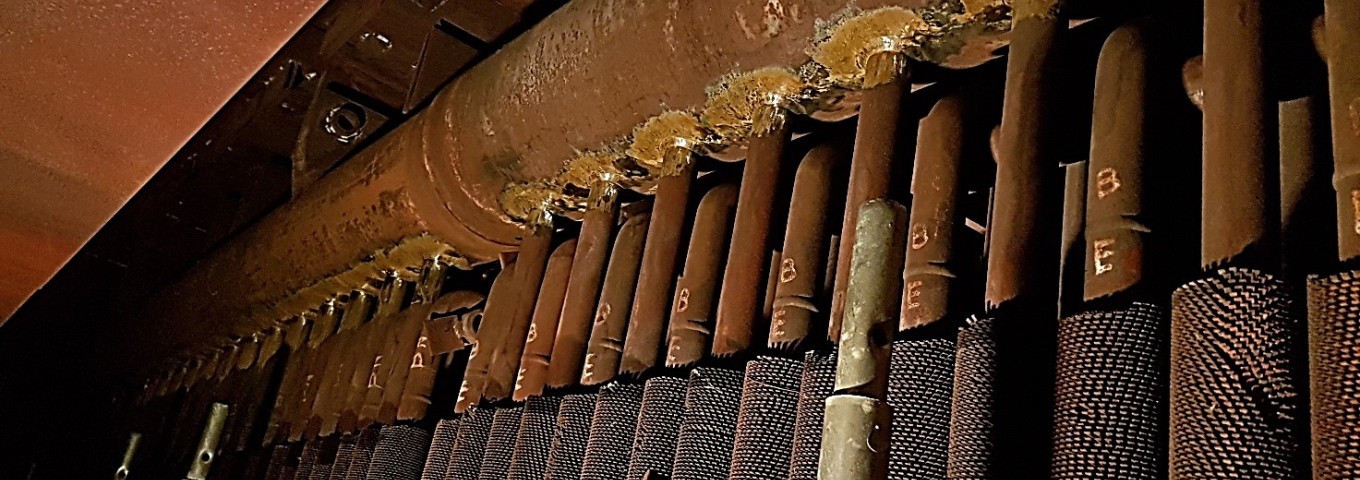
Safety reasons require strict tests of the pressure components of a steam generator to rule out material problems and defects within the structures, which can cause permanent damage, unexpected stops, dangerous accidents and increase in maintenance costs.
Our service can determine the safety and integrity of your equipment, help avoid catastrophic damage and maintain safe and reliable operation over time.
The fully integrated range of services we offer for assessing the condition of a steam generator and HRSG includes:
∙ Practice for prolonging the service, with respect to the design life and calculation of the consumed life, of pressure equipment, subject to the phenomenon of hot creep.
The Italian legislation according to ISPESL circular 48/2003 and subsequent guidelines, UNI 11325-1-2-4 of 2013, requires the mandatory execution of basic non-destructive tests to be carried out jointly with the 100,000 operating hours. micrographic examination with replicas on components of steam generators designed in the creep regime and their repetition at intervals, depending on the results of the previous tests.
∙ Practice for extending the service of steam generators that have reached or exceeded 45 years of age.
Pursuant to ISPESL circular 60/97, steam generators with 45 years of age must be subjected, in order to allow their further safe operation, to specific non-destructive tests, laboratory analysis of materials by removing chips and metallographic examinations to evaluate the mechanical characteristics.
∙ Specialized non-destructive tests to evaluate the structural degradation of welded joints
Control with fluorescent magnetic particles; TOFD and Phased Array for tube weld scanners on HRSG evaporator and superheater manifolds.
Eddy current of shell and tube capacitors.
∙ Inspections and NDT targeted for ten-year checks with elaboration of detailed plans
∙ Field tests and analysis in the FAC monitoring laboratory
∙ NDE / NDT on P91 grade piping
∙ Repair strategies with WPS processing; stability calculations; SBB engineering and evaluation consultancy
Metallurgical sampling of evaporator tubes
This destructive test is useful for providing, after prolonged periods of operation, in-depth information on what could happen inside the generator and on the state of conservation of the evaporator and superheater benches.
When different potential damage mechanisms are indicated (growth of magnetite, corrosion under deposit, FAC, etc.) coming to the correct conclusion and choosing the right course of action is important to save time and costs by minimizing repeated failures and protecting health at long term drive.
∙ Failure Analysis
Damage investigation and root cause analysis.
We effectively identify the underlying causes of damage and failures, offering knowledge and experience to increase the efficiency and operational safety of your generator.
∙ RBI assessment
A priority function of the maintenance service to ensure maximum productivity, becomes the maintenance of the steam generators in full efficiency to limit sudden stops that may derive from malfunctions or breakdowns.
One of the methodologies used is the RISK BASED INSPECTION, as the maintenance intervals are established according to the actual criticality of the components, thus allowing to optimize maintenance costs.
The Donegani Anticorrosione Team, supported in the inspection activities by Italsabi technicians, is able to provide steam generator operators with a practical and timely service capable of satisfying all the aforementioned performances.